Comparés à d'autres matériaux de construction, les caillebotis en acier présentent les avantages suivants : économie de matériaux, réduction des investissements, simplicité de construction, gain de temps et durabilité. L'industrie des caillebotis en acier prend une place importante dans le secteur chinois des structures métalliques. Leur utilisation est de plus en plus courante dans la construction de structures métalliques. Comment prolonger la durée de vie des caillebotis en acier et optimiser l'investissement et le retour sur investissement est un sujet de recherche pour de nombreuses entreprises. Examinons quelques suggestions pour améliorer la durée de vie des caillebotis en acier.
Matériaux et production
La composition chimique et les propriétés mécaniques des matières premières des caillebotis en acier sont des critères importants pour évaluer leur qualité. Seules des matières premières de haute qualité permettent de fabriquer des caillebotis de haute qualité. Leur durée de vie est garantie. Le matériau utilisé est essentiel pour garantir leurs propriétés mécaniques. Les différents paramètres des matières premières (matériau, largeur, épaisseur) doivent être rigoureusement contrôlés afin de garantir une durée de vie prolongée. Les caillebotis en acier soudés à la presse constituent le premier choix pour l'approvisionnement en caillebotis. L'acier plat des caillebotis soudés à la presse est exempt de perforations, leur capacité de charge est préservée et leurs propriétés mécaniques sont supérieures. Les caillebotis en acier soudés à la presse sont soudés mécaniquement, offrant une bonne régularité et des soudures plus solides. Ils présentent une bonne planéité et sont faciles à installer. Ils sont soudés mécaniquement et ne produisent pas de scories de soudage, ce qui les rend plus esthétiques après galvanisation. L'utilisation de caillebotis en acier soudés à la presse est plus garantie que l'achat de caillebotis en acier artificiel et la durée de vie sera plus longue.
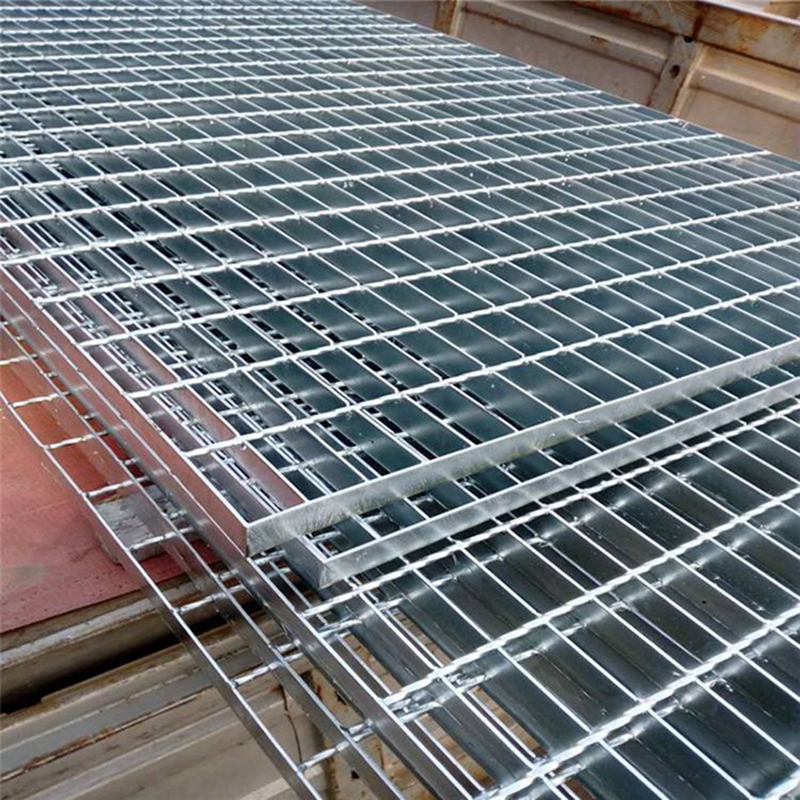
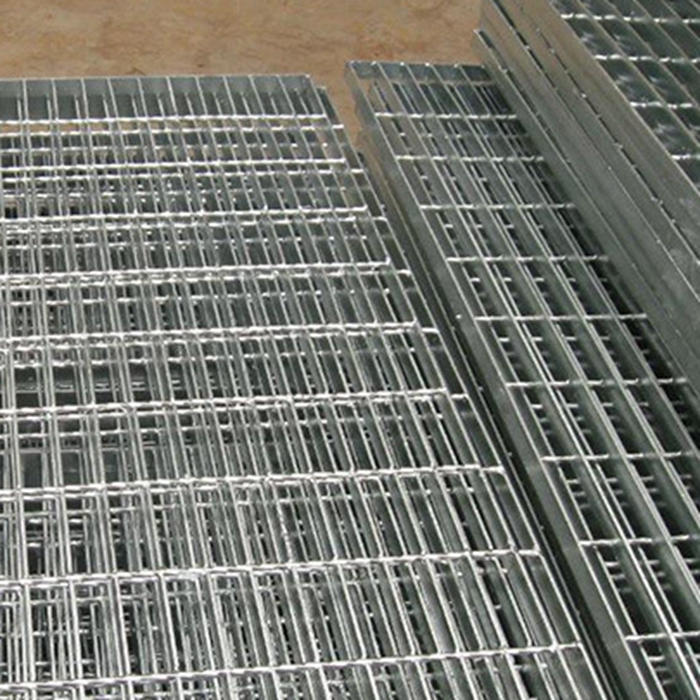
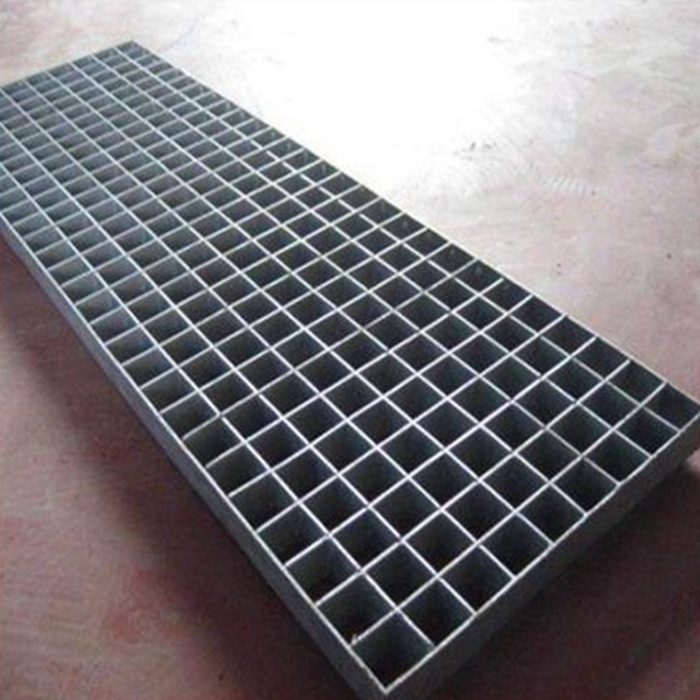

Conception porteuse
Les exigences de charge des caillebotis en acier sont proposées par le bureau d'études et l'utilisateur, ou bien ces derniers sélectionnent directement les spécifications. Le calcul de la relation entre la charge, la portée et la flèche du caillebotis est effectué selon les principes de calcul des structures métalliques. La conception du caillebotis en acier exige qu'en cas de coupure, la surface restante puisse répondre aux exigences de la charge de conception. Une utilisation prolongée modifie les spécifications du caillebotis en acier, entraînant une capacité portante structurelle insuffisante. Par conséquent, le caillebotis en acier ne doit pas être surchargé. Une surcharge entraînerait une déformation du caillebotis et, dans les cas extrêmes, une soudure, voire une détérioration, affectant gravement sa durée de vie. Afin de prolonger la durée de vie du caillebotis en acier, la marge de charge doit être calculée en fonction de l'environnement d'utilisation lors de la conception et de l'achat afin de garantir sa durée de vie.
Corrosion externe
En raison de l'érosion chimique et de la corrosion électrochimique, la section des caillebotis en acier est fragilisée. Il est donc recommandé d'utiliser un traitement de surface par galvanisation à chaud. La galvanisation à chaud est un procédé physico-chimique qui consiste à immerger les pièces traitées dans du zinc liquide en fusion pour former une couche galvanisée, une couche d'alliage et une couche de fusion sur la surface métallique. Il s'agit d'un procédé de protection des matériaux économique et pratique, reconnu dans le monde entier. Le poids et les exigences après galvanisation doivent être conformes à la norme GB/T13912-2002. La galvanisation à chaud de la surface des caillebotis en acier peut en prolonger la durée de vie.
Entretien quotidien
De nombreux facteurs influencent la durée de vie des caillebotis en acier. Pour prolonger cette durée de vie, il est essentiel de veiller à leur entretien. Un entretien quotidien peut prolonger leur durée de vie.
Date de publication : 21 juin 2024